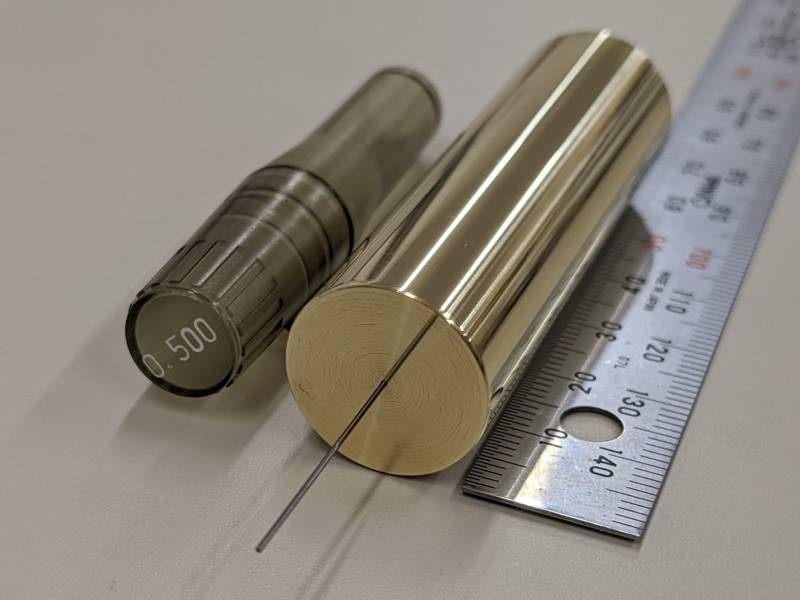
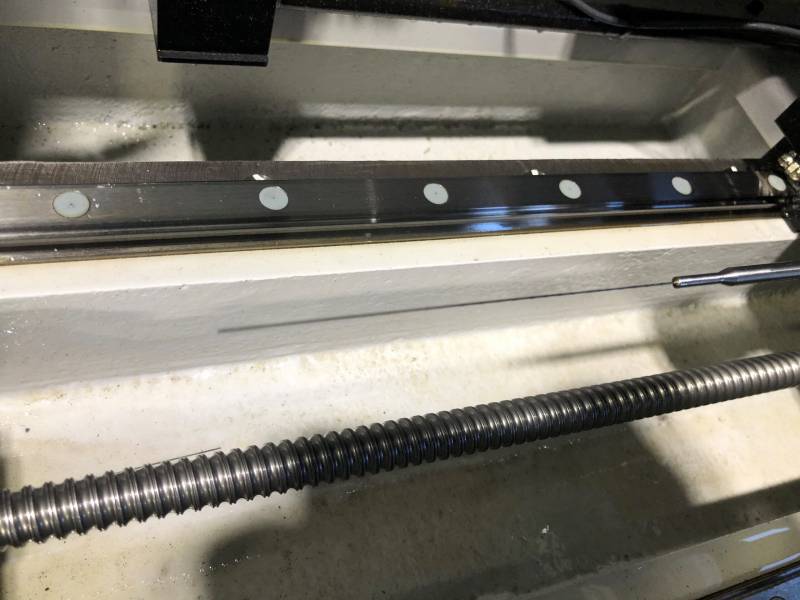
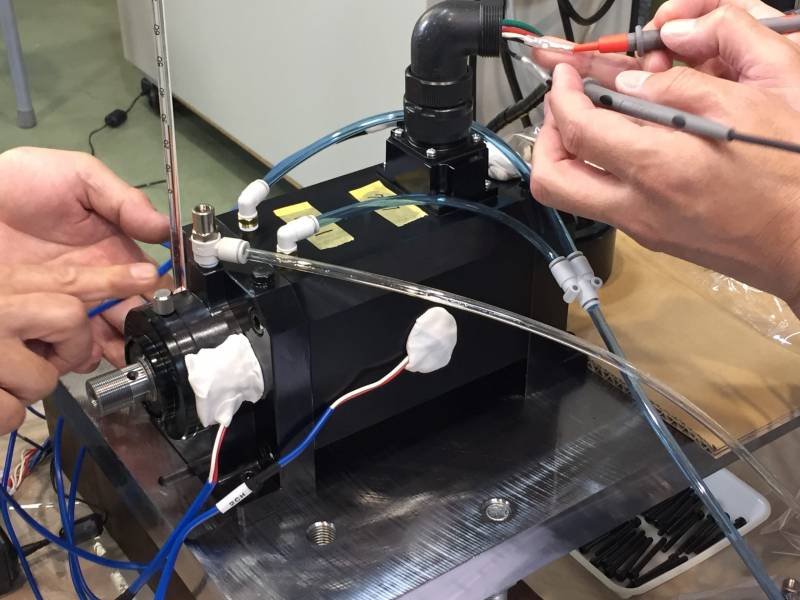
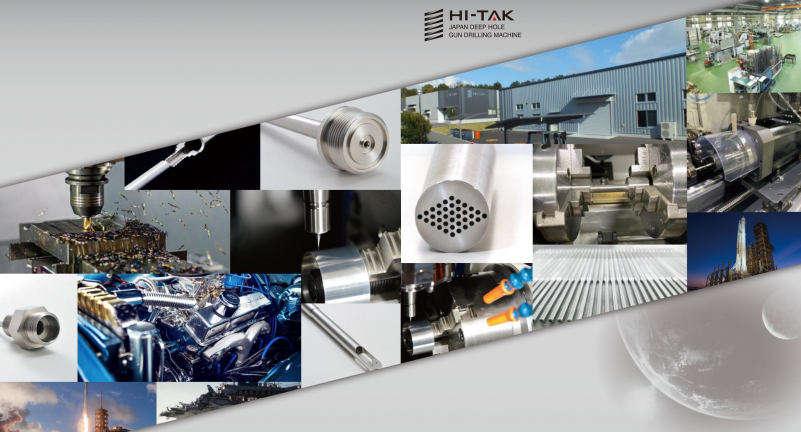
당사에서는, 기존 건드릴 가공으로는 실현할 수 없는 Φ0.5~의 극소경 심혈 가공에도 대응하고 있습니다. 이에 따라 Φ0.5밖에 안 되는 소경 홀에 대해서도 건드릴 가공의 특징인 높은 면조도의 심혈 가공을 실현할 수 있습니다.
2013년도의 모노즈쿠리 보조금으로, 소경에 특화된 구상에 따라 건드릴 머신의 모든 부품을 재검토하여, 수많은 신기구를 담은 신형의 극소경 대응 건드릴 머신을 완성시켰습니다. 이에 따라 당사에서는 기존의 기계로는 대응할 수 없었던 Φ0.5mm의 극소경 심공 가공(심혈 가공)에도 대응할 수 있게 되었습니다.
당사는 소경 전용 건드릴 머신과 심공 가공 기술의 융합으로 Φ1mm에 깊이 400mm, 즉 Φ1mm라는 극소경에 L/D=400의 심공 가공을 실현했습니다. 지금도 당사에서는 이 L/D를 더욱더 연장하고자 기술 개발을 진행하고 있으며, 미개척 영역에 뛰어든 드릴을 이용한 심공 가공의 기술을 날마다 연구하고 있습니다.
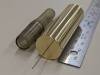
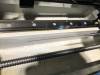
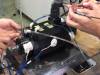
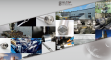
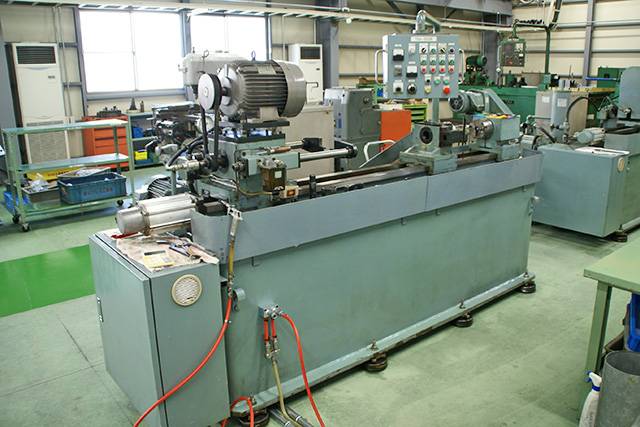
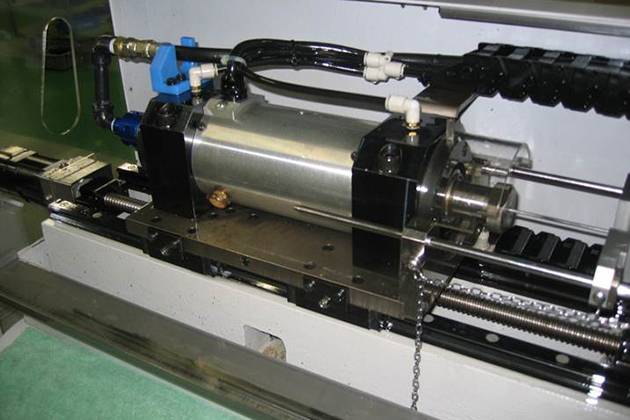
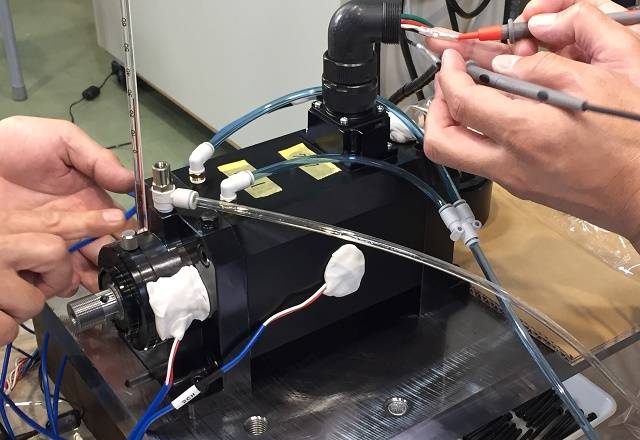
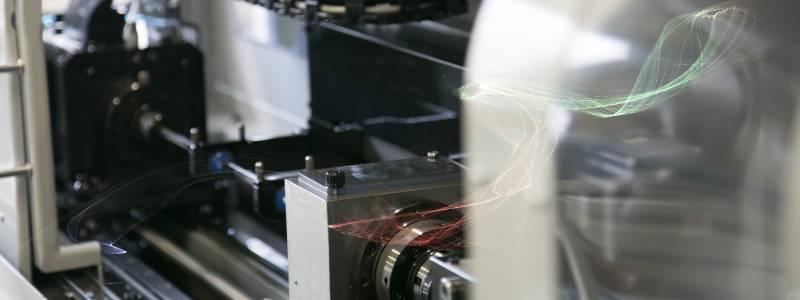
주축 회전…
그것은 절삭 가공에 있어 가장 중요하게 자리매김한다고 볼 수 있다. 그 때문에 당사에서는 건드릴에 몸담기 시작한 당시부터 주축 회전 모터의 개발에 임해 왔다. 당사가 제작한 기존 건드릴은 벨트 구동 방식을 채택하여 사용했었다.
벨트 구동 방식이 뭐지?? 이런 생각을 하신 분도 계실 테니 여기서 잠깐 간단하게 설명해 보자. 벨트 구동 방식이란, 모터 동력을 스핀들로 전달하기 위하여 벨트와 풀리를 사용하여 주축을 회전시키는 구동 방식이다.
공구에 절삭제를 공급해야만 하는 건드릴 머신은, 모터를 별도의 위치에 배치하는 방식이 일반적이었습니다. 하지만 아래와 같은 단점이 있었기 때문에, 당사에서는 새로운 방식의 주축 회전 모터 개발에 임했습니다.
· 벨트&풀리 구동이라서 회전 진동이 주축 자체로 전달되어 버린다.
· 동력의 전달 효율이 나쁘다.
· 높이 방향에 공간이 필요.
· 부품 개수가 많다. (전달 부품 등)
이 문제를 해결하기 위하여 개발한 모터가 중공축에 직접 모터를 설치한 빌트인 모터입니다.
이 타입으로 바꿈으로써,
· 전달 부품을 없애서 진동 감소→회전 정밀도 향상
· 부품 개수 감소→공간 절약을 실현단, 여전히 개량할 점이 남았습니다.
· 인버터(주파수 지령) 제어의 특성상, 회전수 정보가 피드백(회전 정보가 되돌아오는 것)이 없어서 부하 변동 시에 회전 불균형이 생겨 버린다. (가공 시의 부하 변동에 대응 불가능)
· 저속역의 회전 정밀도가 떨어진다.
· 저속역에서 토크가 나오지 않아서 가공 범위가 한정되게 된다.
이러한 개선 항목이 있어서, 당사에서는 2010년 말부터 새로운 스핀들 유닛의 개발에 착수했습니다. 피드백 제어가 되고 저속역부터 토크가 나오는 서보 모터를 주축으로 채택할 수 없을까? 하는 발상으로부터 신형 서보 모터가 탄생했습니다.
· 중공 리졸버 탑재로 회전수의 루프 제어를 행하여 부하 변동 시에도 항상 일정한 회전수를 유지할 수 있다.
· 안정적인 회전 정밀도.
· 저회전부터 최대 토크를 낼 수 있다.
이러한 이점이 있어서, 실제 가공 가능한 홀 직경도 당사 기존 대비 약 2배가 되었습니다.
기존 기계로는 할 수 없었던 난삭재의 심공 가공도 가능해졌습니다.
* 중공 리졸버: 모터의 회전 위치를 검출하기 위한 센서.
* 루프 제어: 출력을 입력에 피드백하는 제어. 이 경우, 회전수 정보를 바탕으로 회전을 제어하는 것.
* 서보 기구(servomechanism)란, 물체의 위치, 방위, 자세 등을 제어량으로 하여 목표치에 추종하도록 자동으로 작동하는 기구. 자동 제어 장치. 서보(Servo)의 어원은 라틴어의 "servus"(영어의 slave·servant라는 뜻).